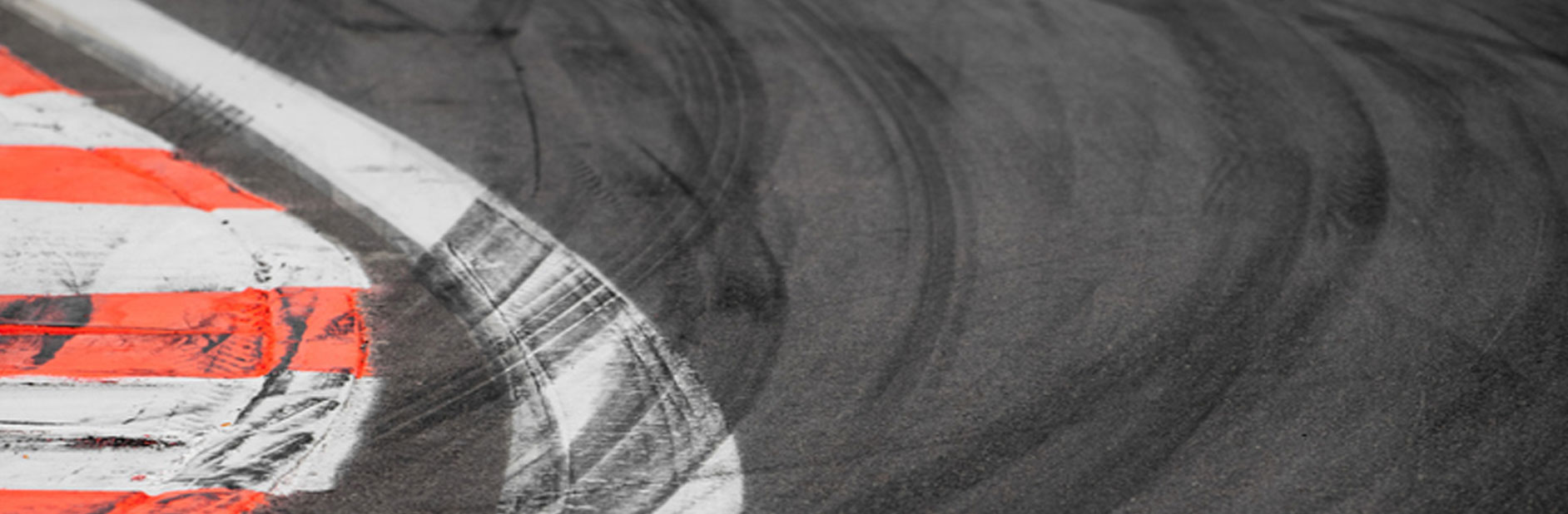
MW Racing
Competition and the desire to excel are what drive MW Racing. That is why we manufacture technically superior engine components that give our customers the winning edge. We provide both custom solutions for elite racing teams and serial production for high performance motorsport. By combining expertise in aerospace technology with precision processes, we are known throughout the world as a leading valve train solutions supplier for customers looking to reach the next level of performance.
MW Racing was formed to bring applied aerospace technology to high-performance combustion engines in the motorsport industry. MW Racing is a brand name and dedicated manufacturing group of MWH, a leader in precision manufacturing for over 160 years and an innovator in the engine world for much of the last century. A family-owned business, MWH and MW Racing are passionate about innovative engineering in the development of high quality valve train systems. Together, we are committed to providing leading-edge solutions to help customers achieve the best possible engine performance. And to win!

Performance
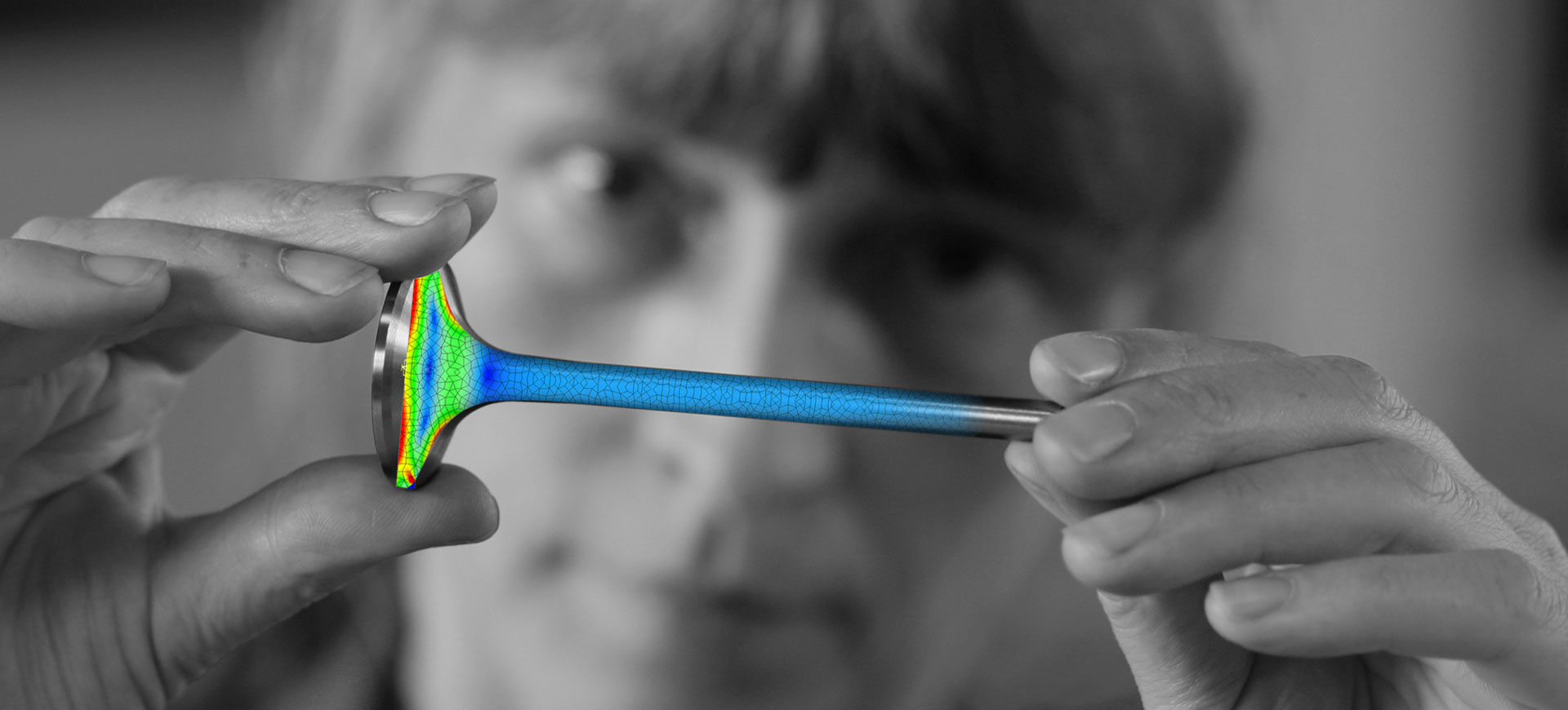
WELCOME TO THE CENTER OF RACING INNOVATION
Improving engine performance is what puts you in the winner’s circle. It is also what drives MW Racing to create new materials and manufacturing processes to get you there. The center of that effort is the MW Racing Innovation Center, where our engineers create and test the next generation of materials, coatings, and components.
State-of-the-art research, design, and development resources, including material deformation visualization, 3-D system modeling and finite element (FE) analysis are available to all customers. No matter what the challenge, MW Racing works with our customers to develop customized, cutting-edge solutions that meet your needs.


Design + Analysis
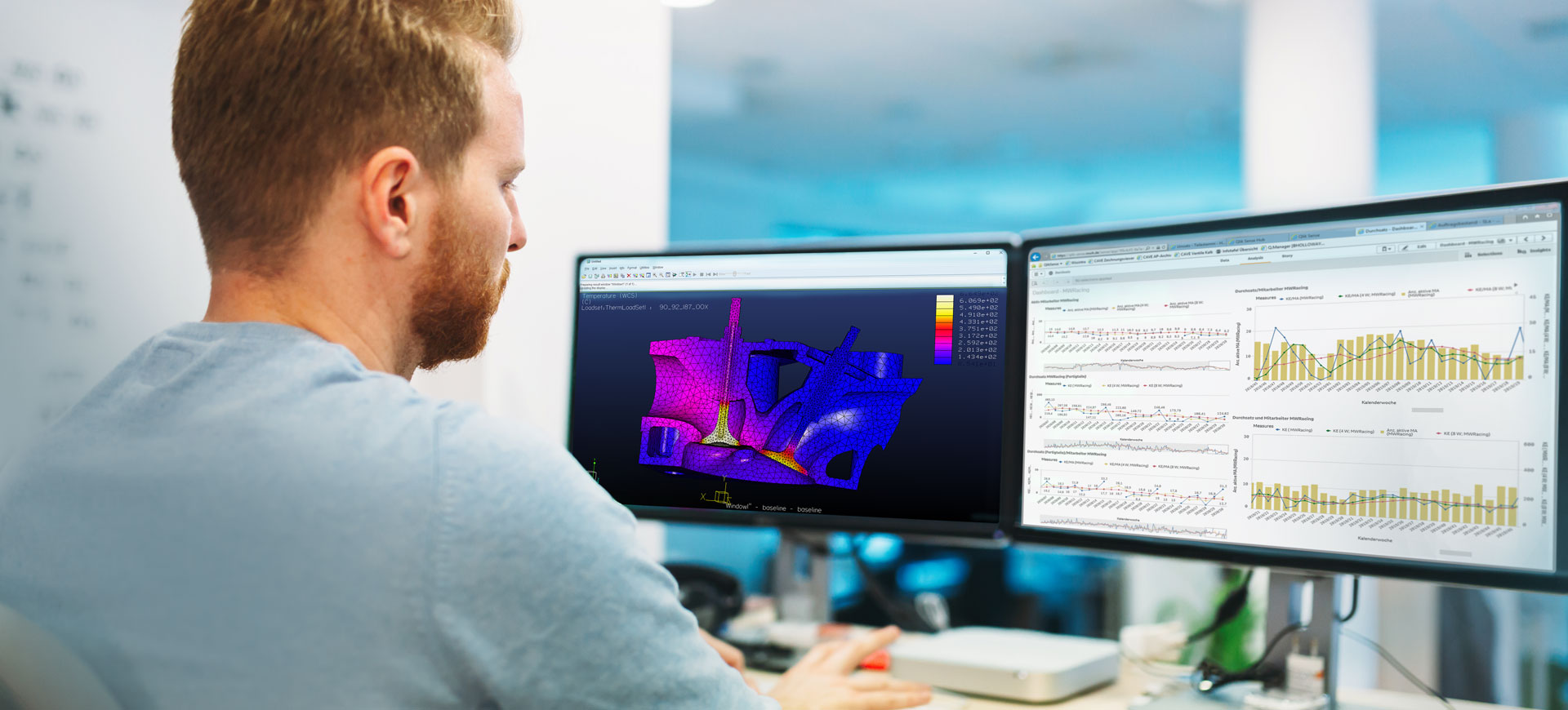
A TRACK RECORD FOR ENGINEERING EXCELLENCE
MW Racing engineers work closely with your engineering team to consistently achieve breakthroughs in materials, processes, products and coatings. These include extruded alloys with increased fatigue properties, our gamma Titanium Aluminide for unparalleled stiffness and minimum weight, and thermal barrier coatings to extend operating ranges of components. Our coating test rig helps us develop new coatings. We evaluate their performance to ensure
optimal wear and friction characteristics. MW Racing development programs continue to push the limits of what is possible.
MW Racing’s reputation as an industry leader comes from sharing our customers’ passion for innovation. We collaborate with top car and motorcycle race teams and OEMs worldwide to provide custom design and analysis solutions that fit their unique needs.

Materials
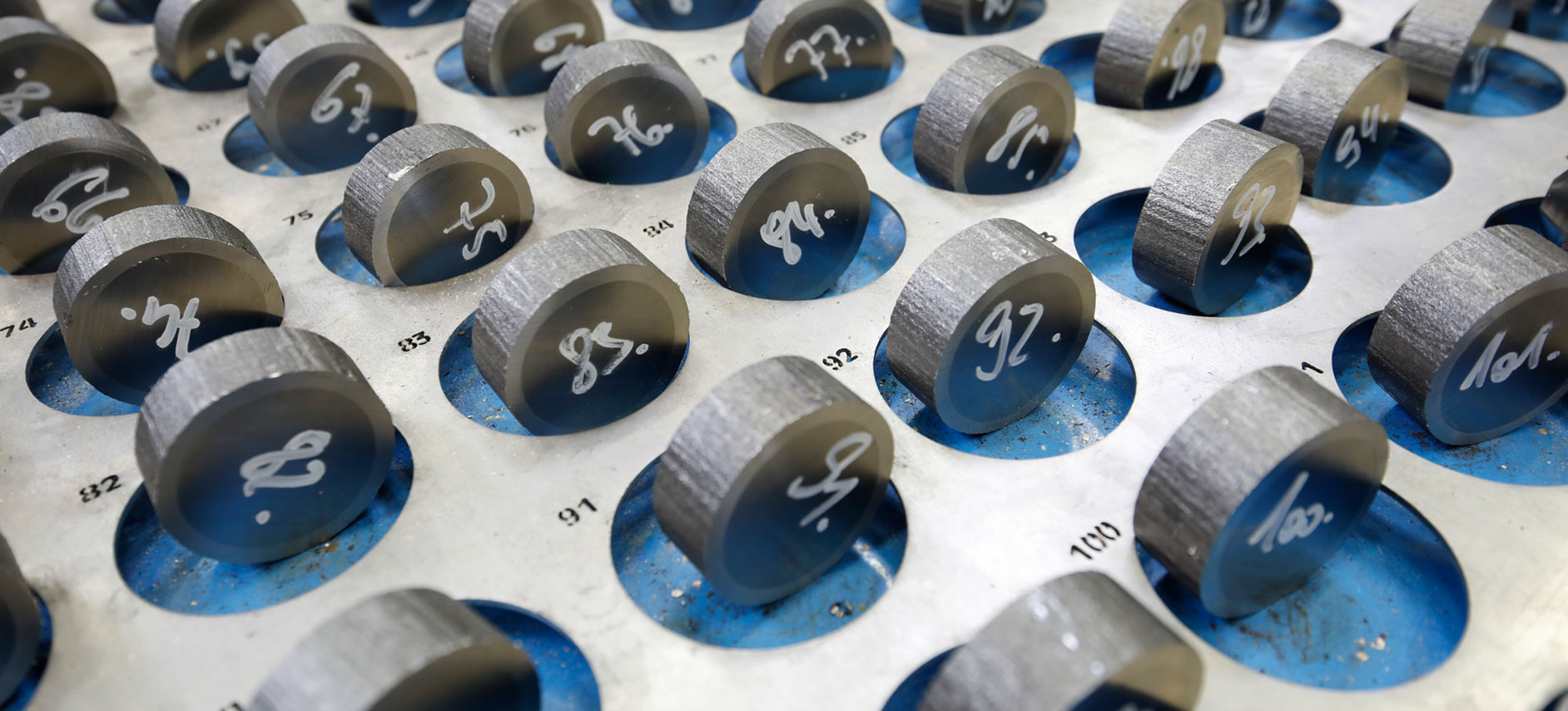
PERFORMANCE COMES FROM WITHIN
Success on the track depends on what goes into your engine. MW Racing’s superior materials and proprietary processes are critical in extending the boundaries of speed and engine life. Only MW Racing has developed extrusion technologies for gamma Titanium Aluminide, bespoke extruded Titanium alloys, Nickel superalloys, and steels.
You can rely on MW Racing to manufacture your engine components using state of the art materials and methods that achieve unsurpassed thermal and mechanical performance. It’s not only the range of materials we offer, it’s knowing how to use them.

Manufacturing
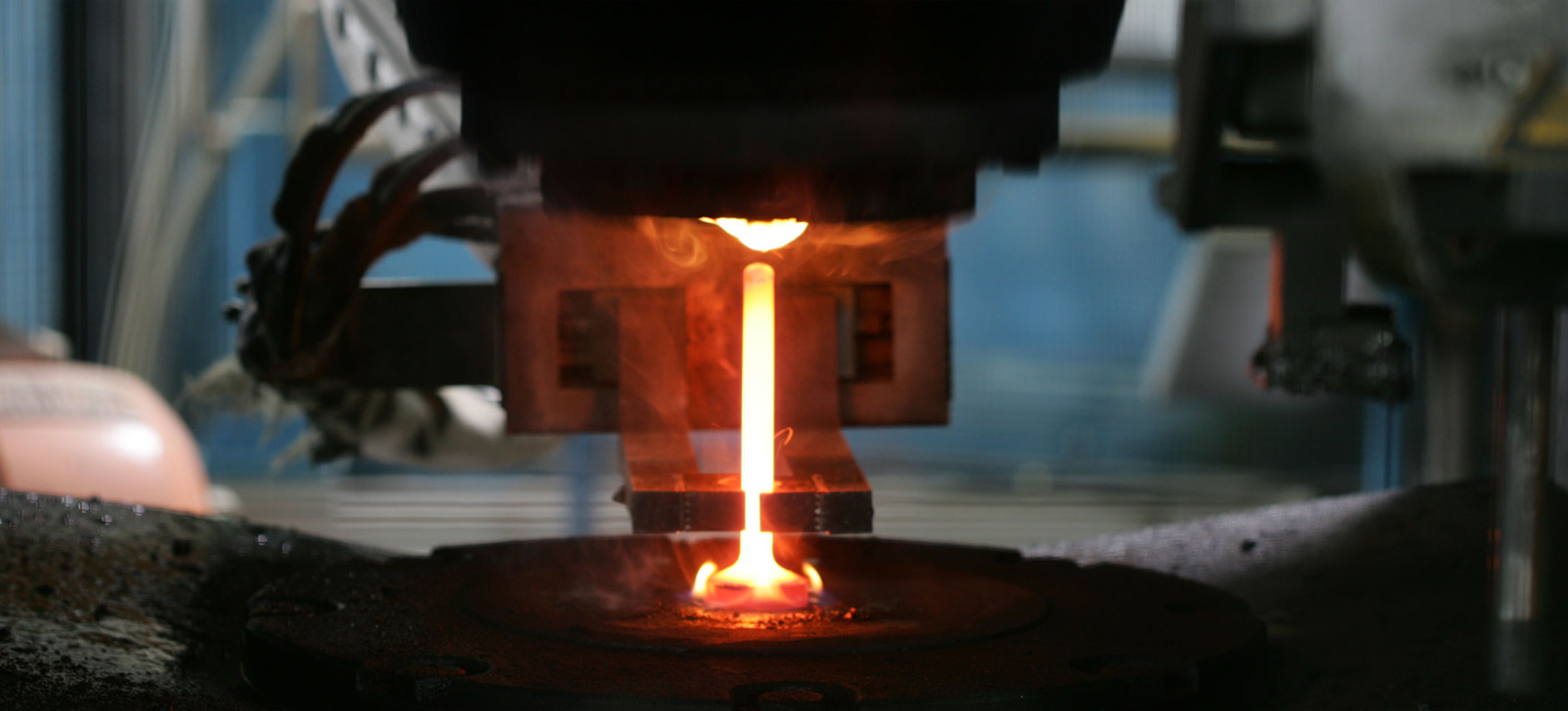
WHERE METALLURGY MEETS MANUFACTURING PRECISION
MW Racing manufactures the strongest, most durable engine components in the racing industry — some of which were originally designed for the aerospace industry. Our proprietary extrusion and manufacturing processes greatly enhance the mechanical proprieties of metal alloys. We have developed extrusion processes that not only increase the elastic modulus of Titanium alloys but also produce one-piece parts without friction or welds. In our Grossbodungen facility, we can handle batches from 1 to 1,000 parts.
You won’t find MW Racing products in a catalog. Instead, you’ll find flexible production that’s tailored to meet your needs. We work with you to provide custom solutions manufactured to your precise specifications to create winning components. You’ll never worry whether a short lead-time order will slow high volume production. We are on the line to deliver the quality parts you want, in the quantities you need, on the schedule you desire.

Coatings
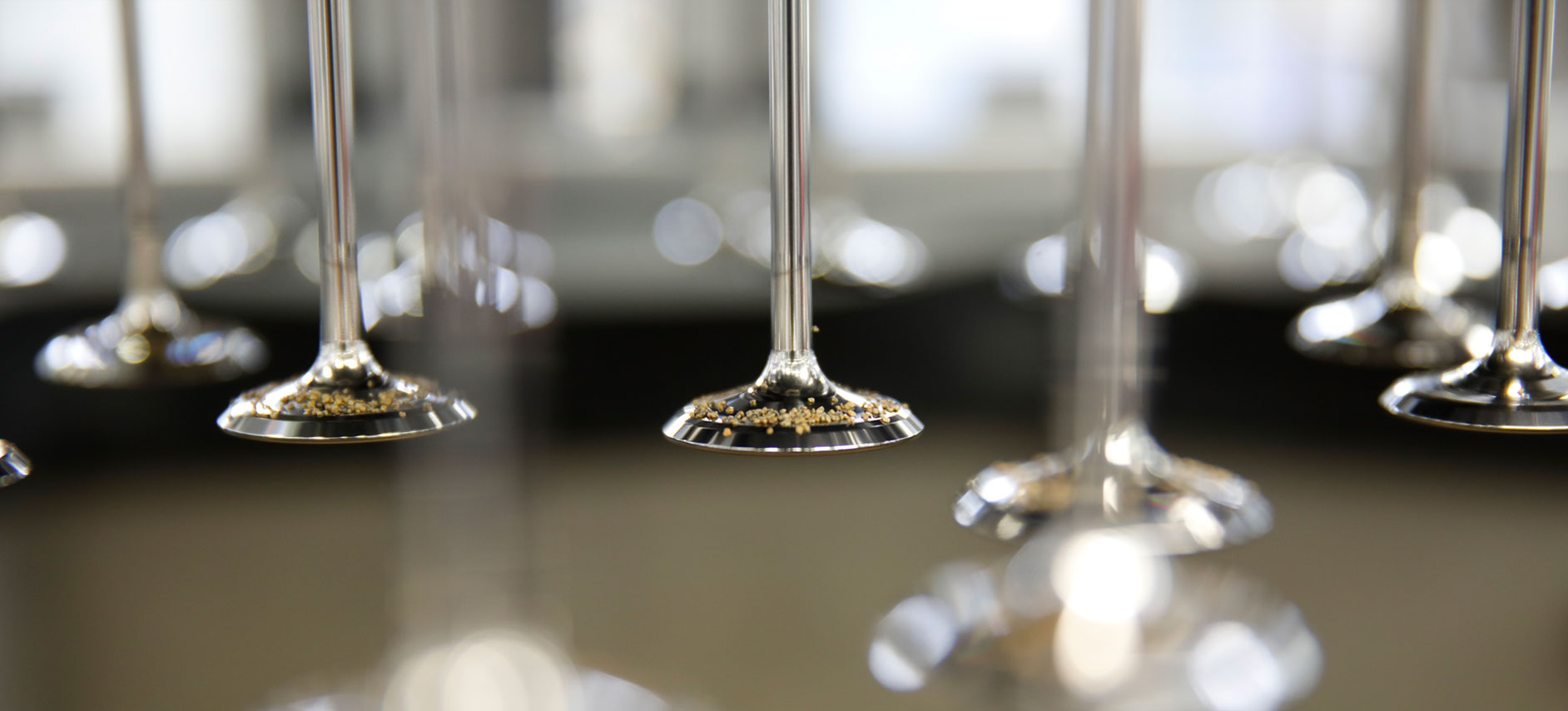
PERFECT COATING IS OUR STANDARD
High performance valve train solutions start with the optimal material and finish with the perfect coating. MW Racing has the largest offering of valve materials in the industry, and we own our own innovative coating facility. MW Racing coatings reduce friction and increase component life. We offer in-house PVD coatings such as DLC and CrN. While other manufacturers ship components off to coating facilities, MW Racing does everything under one roof to guarantee the highest standards of quality and reliability.
DLC:
- lowest friction coefficient
- exceptional high adhesion
- toughness
- nanogradient structure
- suitable for inlet and exhaust valves
- ideal for piston pins
CrN:
- all-purpose valve coating
- low friction and wear
- high adhesion and hardness
- high temperature resistance
- suitable for inlet and exhaust valves

Quality
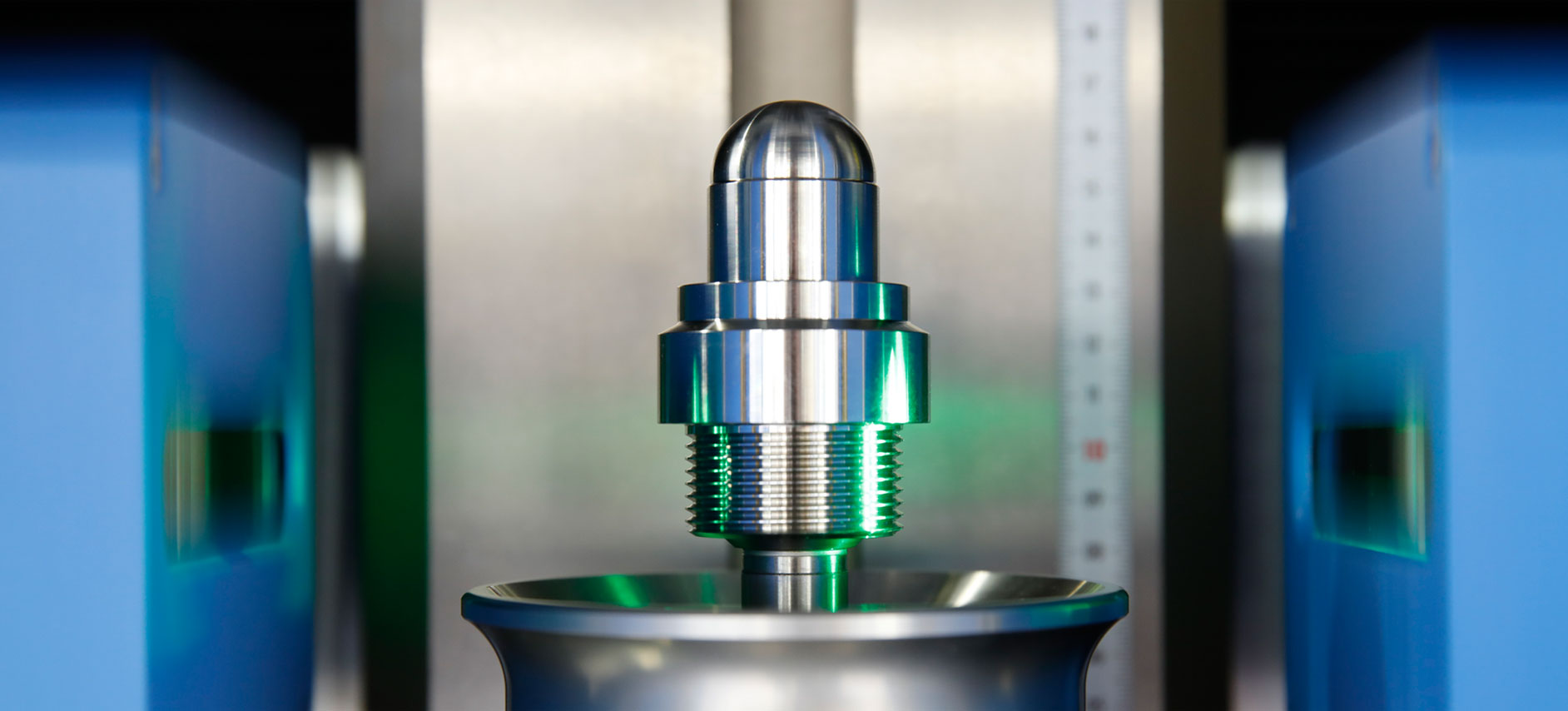
BUILT TO REACH PERFECTION
Quality has been built into our processes and company culture for over 160 years. Every component we deliver undergoes an exhaustive series of control steps including visual, optical, dye penetration and coating analysis. In addition to these stringent quality checks, all Titanium Aluminide products undergo chemical analysis, ultrasonic and Eddy current tests.
We offer component serialization with 100% traceability back to material lots, forging and heat treatment, and manufacturing operations. Quality is not just something we check; it is what we live and breathe.