TECHNICAL BULLETIN
Sustainable chrome plating at Märkisches Werk GmbH replaces open bath process. High-end chrome plating facility is ready for production.
HALVER, GERMANY - December 11, 2023 -
To our valued customers,
Continuous implementation of highly innovative processes is part of Märkisches Werk’s (MWH) sustainability philosophy. This enables us to improve digitalization and automation, which leads to robust production processes and ensures the highest quality products.
Surface treatment is one of the key production processes of high performance valve train components for less wear and highest corrosion protection. In particular, galvanic hard chrome plating is applied to a wide range of valve spindles for your most demanding applications. Since 1976, our main valve plant in Halver has plated more than 10 million valves using an open bath electrochemical deposition process.
However, conventional chromium plating facilities face increasing health and environmental impacts. Facilities with open baths using chromium trioxide (CrO3) are known emitters of Cr(VI) into the environment. The European Chemicals Agency (ECHA) has formulated strict regulations in the REACH act, which rates CrO3 as “substance of very high concern” (SVHC). In fact, the use of CrO3 containing substances for hard chrome plating is only permitted for authorized users and, to gain authorization beyond 2024, MWH has been participating in the CTACSub2 consortium.
Aiming to provide best quality products at the lowest possible environmental impact, MWH has recently implemented a new chrome plating facility for production of large 4-stroke valve spindles (Figure 1). A smaller scale version of the same technology has been used in the production of valve spindles at our plant in Großbodungen for more than 10 years.
Both facilities are ready for the future:
- The unique and patented systems allow chrome plating without the accumulation of wastewater.
- The closed loop system for product cleaning and plating results in minimal atmospheric emissions.
- During the process, the chromic acid is drawn past the valve by creating a negative pressure. This has the advantage that the chrome liquid flow stops immediately in the event of a leak because the system draws air. In this way, the risk to employees and the impact on the environment is reduced to zero.
- Additionally, electrolyte usage is reduced significantly since each valve is plated in individual cells.
- The technology also allows for the substitution of Cr(VI) via non-toxic Cr(III) in the future, once this non-toxic compound is ready for commercial use.
- The process technology itself, an electrochemical deposition of chrome, remains the same to achieve less wear and highest corrosion protection.
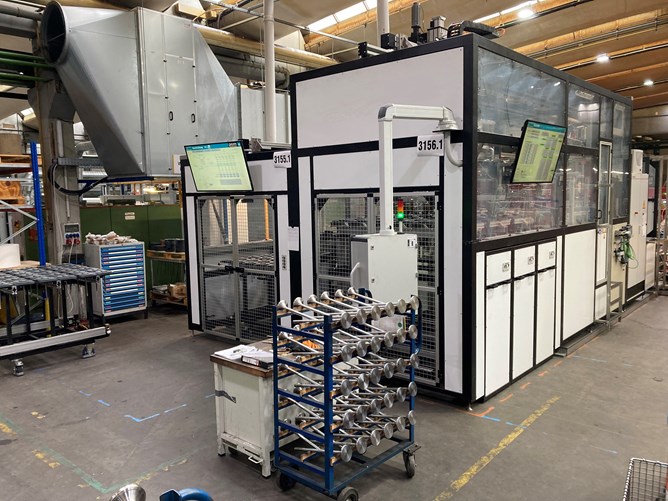
The new facility will completely replace open bath chrome plating, which has been an industry standard since decades. This upgrade is a mandatory step on our path to a sustainable and REACH-conforming future of galvanic surface treatment. The open bath facility will be used for the final time in February 2024. Switching valves over to the new production facility may require minor dimensional adjustments to the chrome plating thickness and/or chrome run-out dimensions. Based on negative pressure applied, there will also be a relatively slight variation in visual appearance of the chrome plating.
For part-specific information, including chrome layer thickness and run-out, please refer to your corresponding MWH manufacturing drawing(s). In case of questions or need for consultation, please feel free to contact your corresponding MW sales manager. We very much appreciate your support during the implementation and thank you for helping to ensure the well-being of our employees and reduce the environmental impact of our business.
Link: https://www.mwh.de/en/news/#New, sustainable chrome plating at MWH